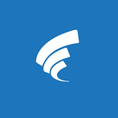
Stock Control
Ensure your business’ stock is kept up to date in real-time and fully integrated with the Sage 50 Products module.
With Cim50 Stock Control...
- Track all batch and serial number movements, showing a detailed history and costing breakdown across the manufacturing process.
- Process all transaction types from one integrated system including receipt of goods, despatching finished items and stock adjustments.
- Utilise the available fields in the Sage 50 Accounts Products along with additional Cim50 Stock Control fields with all amendments recorded.
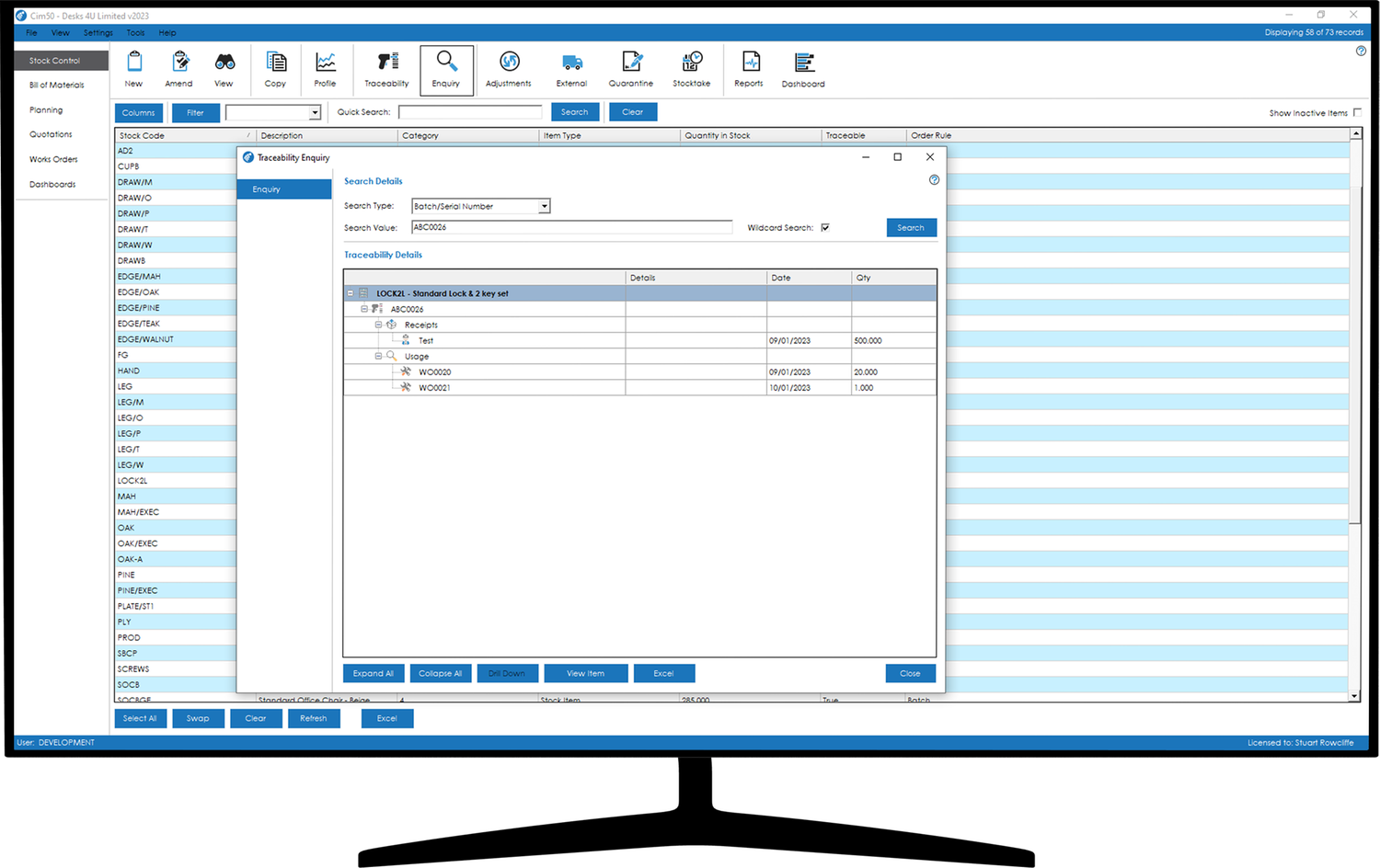
Key Features & Functionality
- Traceability
- Stock Profile
- Stocktake
- Quarantine
- KPIs and Dashboards
- Audit Log
- Alternative Suppliers
- Multiple Units of Measure
- Amend Goods Receipt
- Certificates of Conformity
Bill of Materials
Configure your built items with advanced functionality that fully integrates with Sage 50 Accounts.
With Cim50 Bill of Materials...
- Improve profitability by accurately calculating the cost of bill of materials including material, labour and machine overheads with full costing history.
- Configure your built items to meet all necessary manufacturing specifications, no matter the complexity or number of components.
- Verify there is enough stock to assemble multiple bill of materials, review machine & labour requirements and record built items.
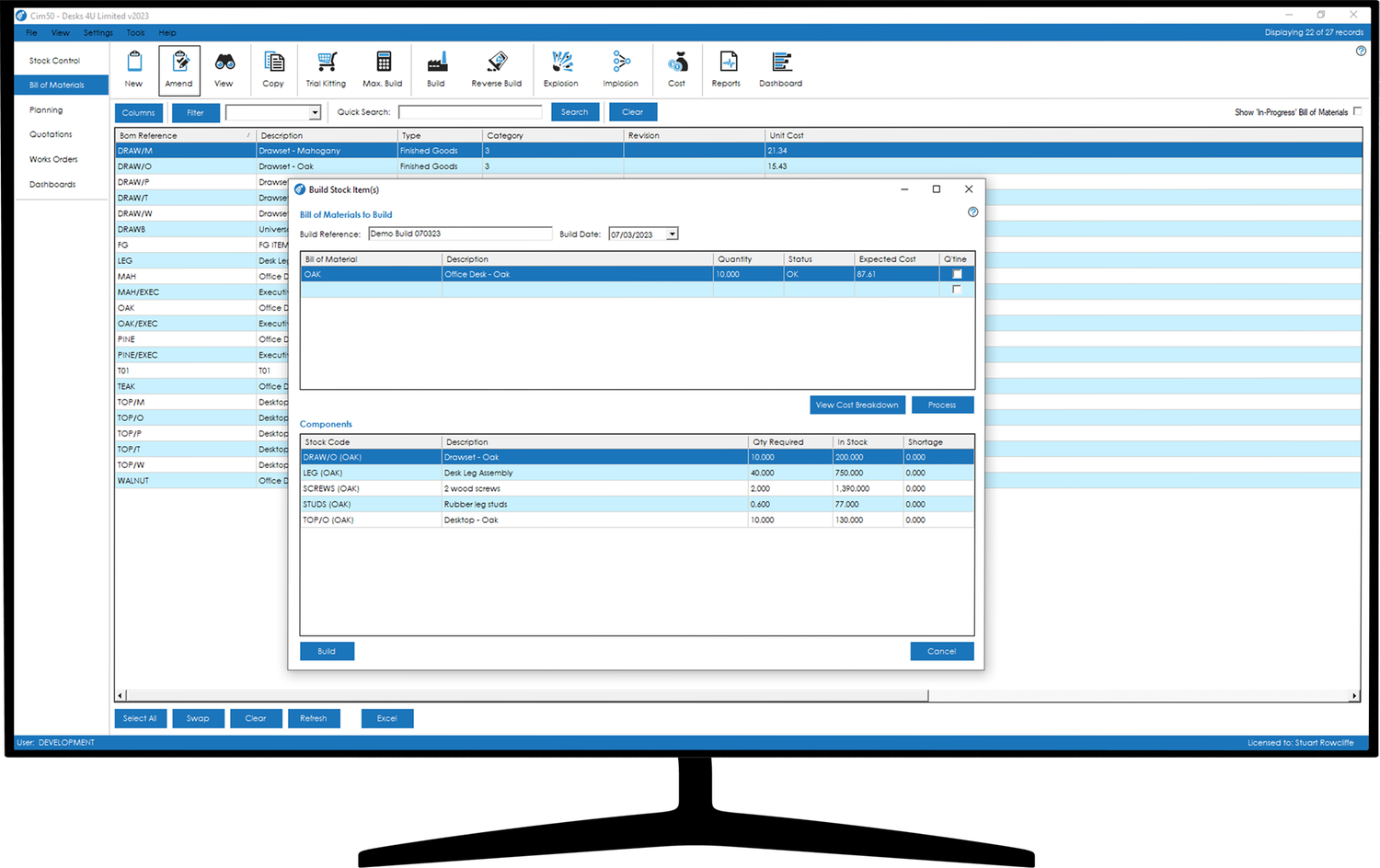
Key Features & Functionality
- Trial Kitting
- Costing
- Drawings & Attachments
- Subcontract Costing
- Operation Components
- Audit Log
- Max Build
- Explosion/Implosion
- Reverse Build
- Build
Works Orders
Control built products through each stage of the manufacturing process with Cim50’s Works Orders module, integrated with Sage 50 Accounts.
With Cim50 Works Orders...
- Ensure costs are accurate and remain within budget by tracking material, labour, machine, subcontract, tooling and overhead costs.
- Review rough cut resource availability and produce shop floor paperwork with detailed instructions and times.
- Allocate and issue components to production to facilitate accurate stock holdings and comprehensive WIP reporting.
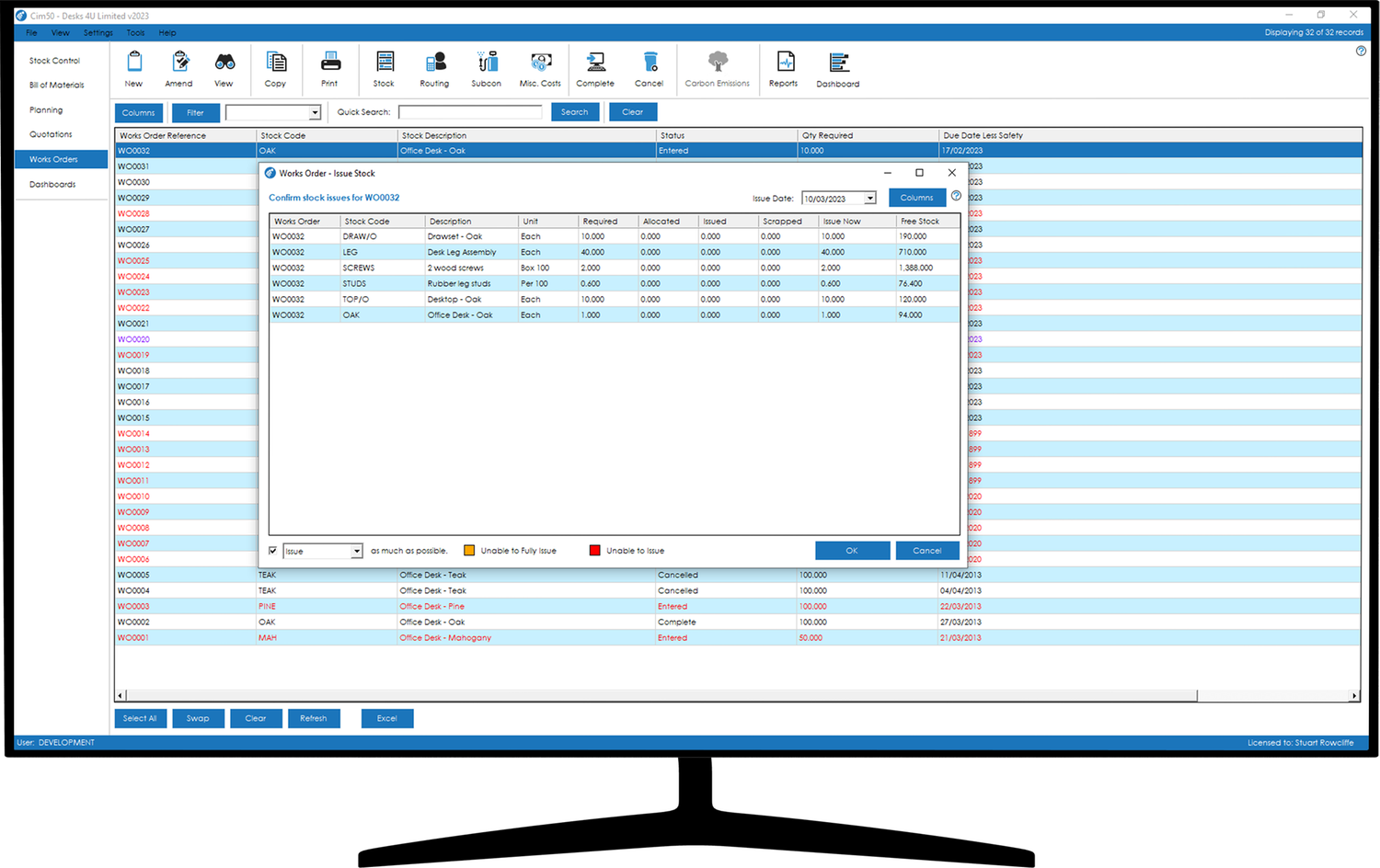
Key Features & Functionality
- Carbon Emissions
- Work To List
- Audit Log
- Labour Bookings
- Costing
- One Off Works Orders
- Subcontracting
- Capacity Planning
- Shop Floor Documentation
- Work in Progress
Planning
Calculate the materials needed to manufacture products and meet customer demands with Cim50’s Planning module, integrated with Sage 50 Accounts.
With Cim50 Planning...
- Identify purchase and manufacture recommendations based on current demand versus stock on hand and outstanding orders.
- Ensure demands can be satisfied with software that reads from sales orders, sales forecasts, works orders, reorder levels and make to stock.
- Set up individual stock items with pre-requisites such as reorder rules and lead times to only buy and manufacture what you need, when you need it.
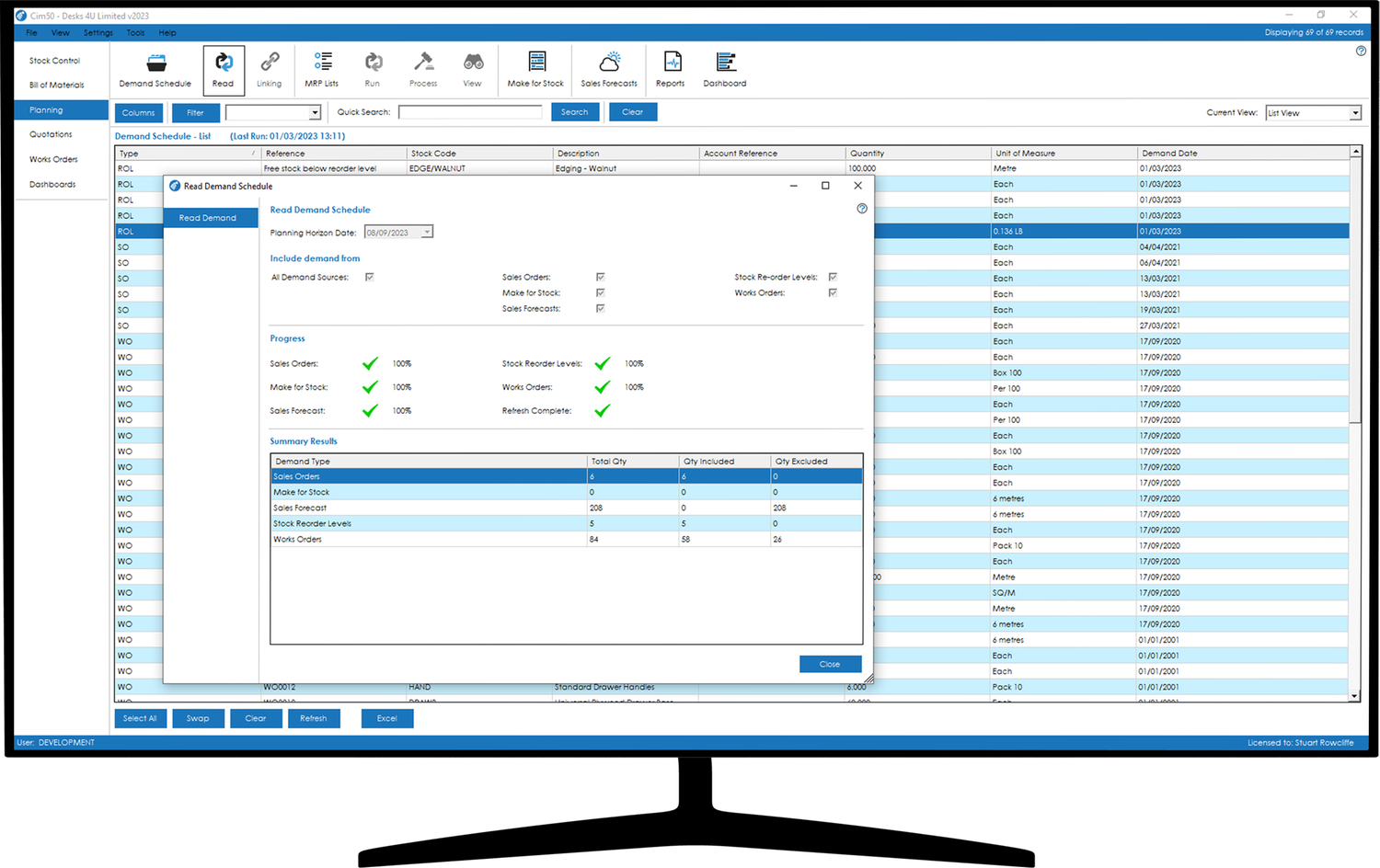
Key Features & Functionality
- Just in Time
- Demand Schedule
- MRP
- Sales Forecast
- Make to Stock
- Rescheduling
- Dashboards
- Resource Calendar
- Schedule Planning
- Aggregating Demand
Quotations
Estimate costs and calculate total selling prices for manufactured items with Cim50’s Quotation module, integrated with Sage 50 Accounts.
With Cim50 Quotations...
- Copy quotations to track amendments from customers & prospects and update costings based on latest prices whilst maintaining all previous revisions.
- Utilise full visibility of costs, revenue and expected profit margin broken down by material, labour, machine, overheads and subcontract,
- Automatically calculate sales prices for quote items based on cost mark-up, profit margin or on a fixed price basis and price for multiple quantities.
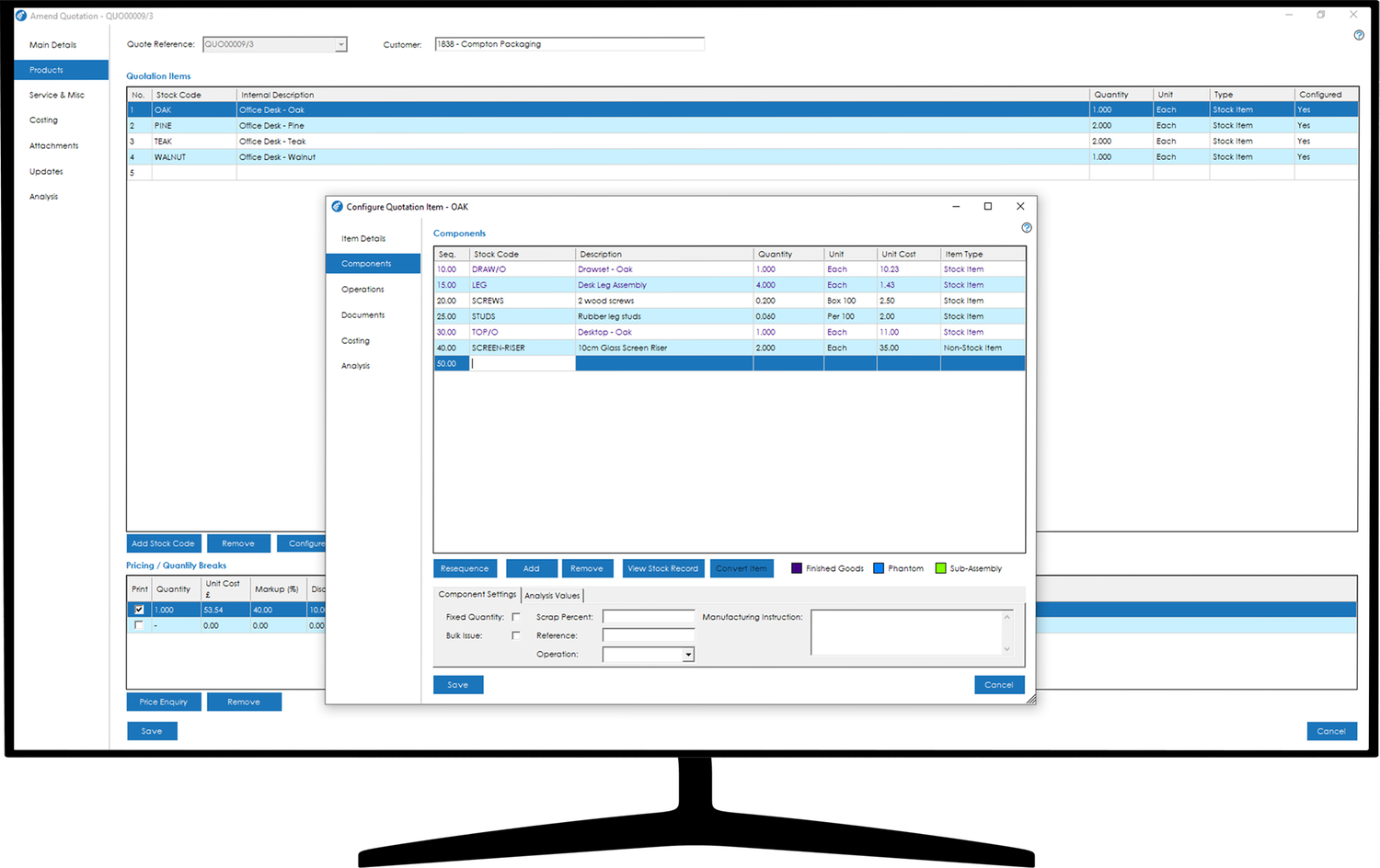
Key Features & Functionality
- Pricing
- Configure Built Items
- Revision History
- Products & Services
- Documentation
- Profit & Loss
- Order Processing
- Quantity Breaks
- Discounting
- Prospect Quotes
Shop Floor Data Capture
Carry out all stock transactions and operation times using a barcode scanner with Cim50’s Shop Floor Data Capture module, integrated with Sage 50 Accounts.
With Cim50 Shop Floor Data Capture...
- Capture times for works orders operations and monitor employee productivity in real time to maintain manufacturing profitability.
- Using the power of barcoding, allocate and issue stock to works orders, manage subcontract processes and complete items into stock.
- Accurately carry out any stock movement from purchase order receipt to sales order despatch (and all movements in between) using a barcode scanner.
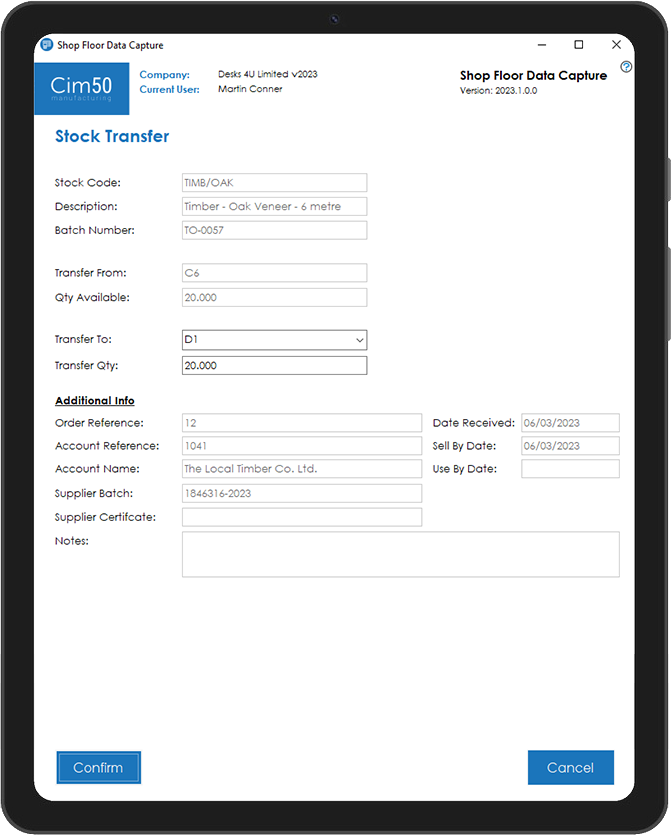
Key Features & Functionality
- Quarantine Inspection
- Works Order Completion
- Subcontract
- Operation Processing
- Works Order Materials
- Bom Build
- Stock Take
- Despatch
- Goods Receipt
- Stock Movements
Graphical Scheduler
Visualise your production schedule and control your shopfloor workload with an easy-to-use interface.
With the Cim50 Graphical Scheduler…
- Group your resources and schedule production based on the capacity and availability of labour resources, machine resources or both.
- Quickly see shopfloor workload and take control of your production plan to improve your manufacturing efficiency.
- Predict and resolve future conflicts and overloads to optimise the production plan to meet customer demands.
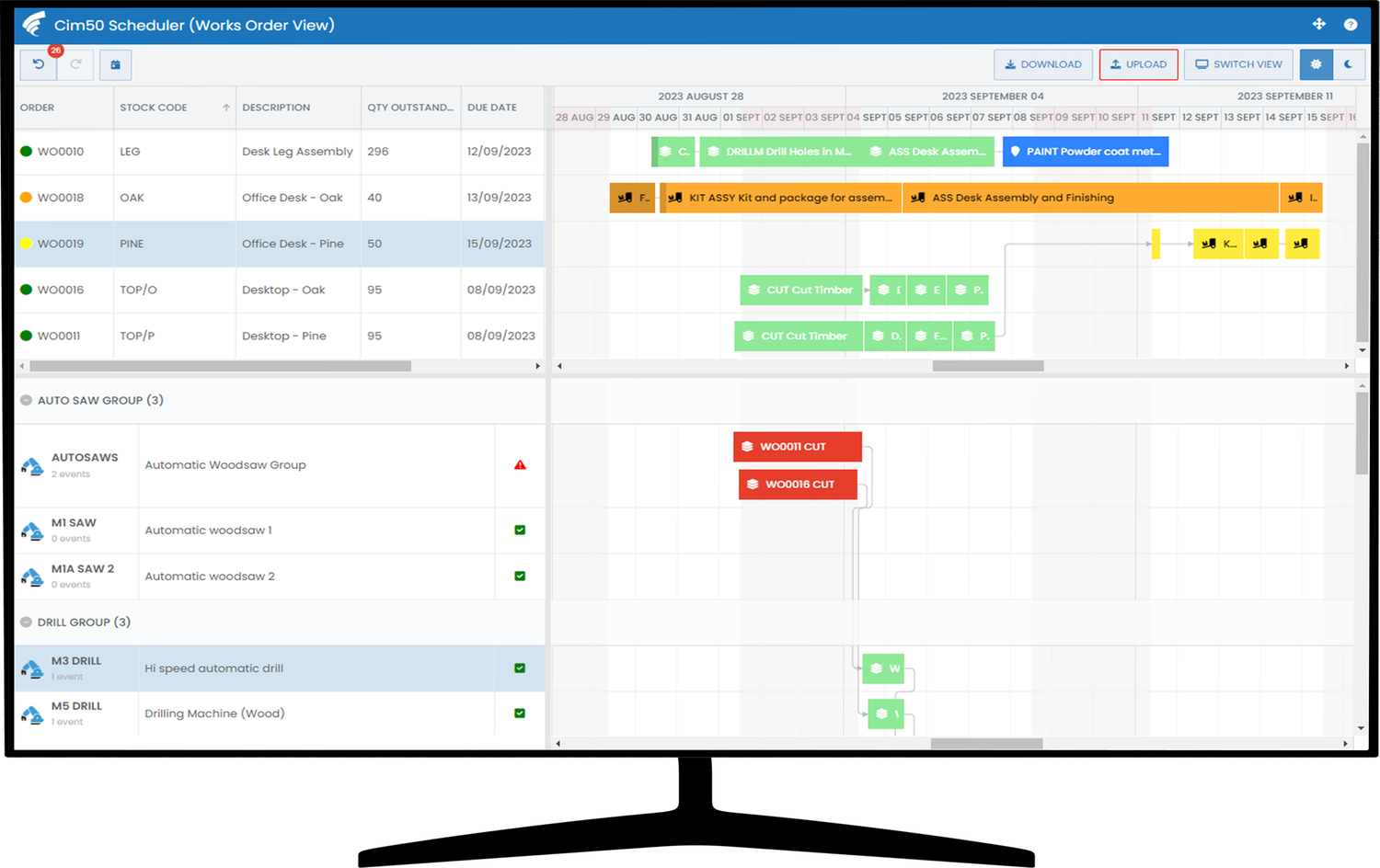
Key Features & Functionality
- Conflict Management
- Works Order Planning
- Resource Utilisation
- Dynamic Colour Coding
- Dependency Management
- Lock Works Orders and Operations
- Review Cim50 Works Order Details
- Schedule by Labour, Machine or Both
- Resource Grouping
- Multiple Planning Calendars