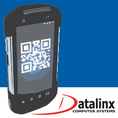
Warehouse Manager for Sage X3
Mobile Devices for Barcode Scanners
Datalinx has an extensive range of tested and approved devices that are compatible for use with Warehouse Manager. These range across the Android, Windows Mobile and Windows CE operating platforms.
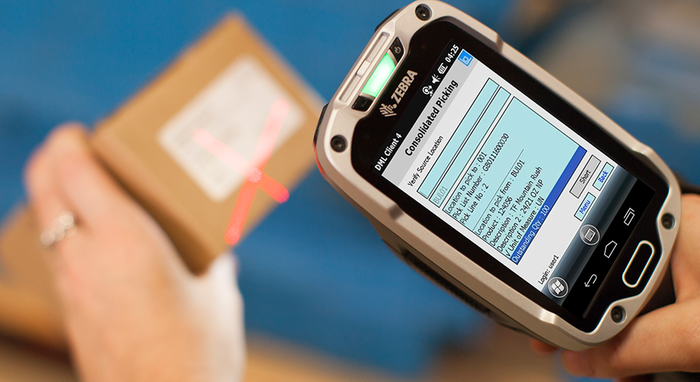
Sales Order Picking
For many warehouses, particularly in distribution and the supply chain, sales order picking is utilised to prepare products for dispatch. Combining Sage X3 and Datalinx Warehouse Manager delivers a solution that will ensure high efficiencies and accuracies of picking and dispatching product with the associated reductions in costs. Pick Tickets and Lists are created and authorised within Sage using the standard system functionality.
Pick Ticket and Hand Held Scanners
- Once authorised for picking by Sage, the details of the pick ticket will be available for display on the hand held scanner within the warehouse. These units will guide the operative to the appropriate bin advising the quantity and product to pick. Once correctly completed on the hand held, Sage is updated as the action occurs in real time.
- Functionality includes:
- Guided by priority
- Pick by physical properties
- Unique 'pick and hold' facility
- Marshal order prior to despatch
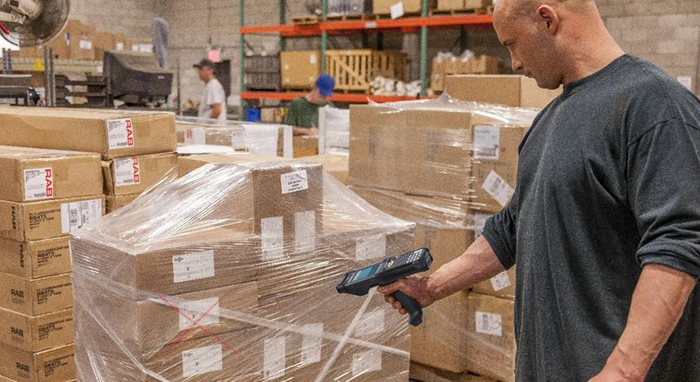
Dynamic Stock Counts
This Datalinx module provides a true perpetual inventory model, to allow stock counts to take place as required, rather than on an annual basis. This ensures minimal disruption to the business, reducing cost as the warehouse stays operational even during a count, thereby increasing efficiency.
With Warehouse Manager Dynamic Stock Take, there is no requirement to lock the count area, leaving it operational throughout the stock take, except for the short period when the specific location is being counted.
Multi-count and recount options are enabled on the scanners, as is the ability to handle “discovered stock,” stock in unexpected locations, and zero counting when stock cannot be found.
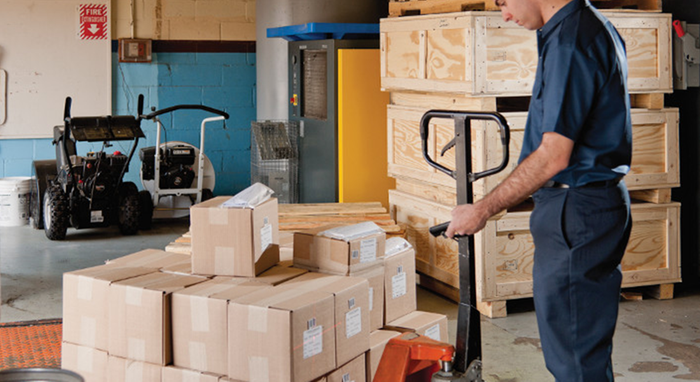
Packing and the Pack Bench
The Datalinx Pack Bench provides dedicated functionality that assists and directs users to re-verify picked orders and automate the production of despatch notes and associated documentation. Box contents are recorded against specific boxes and box types can be set and defined in Sage X3.
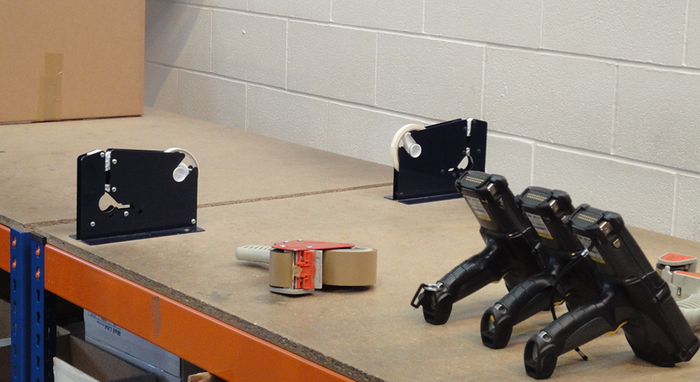
Transfers and Warehouse Operations
Bin to bin / location to location
Batch / serial number traceability
Product code across multiple references
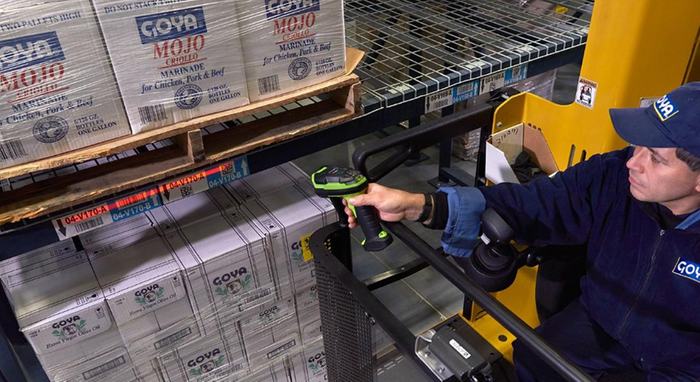
Lots, Serial Numbers and GS1 Barcodes
The use of GS1-128 codes is increasingly becoming an industry standard in areas such as healthcare, pharmaceuticals, food service and manufacturing. Compatibility within Datalinx is standard and complex data can be recorded. When these are used to scan product, pick and put-away times are reduced due to only a single barcode needing to be scanned rather than more time consuming multiple product codes. The resulting stock movement and transaction is then updated as standard with Datalinx Warehouse Manager in real time into Sage X3.
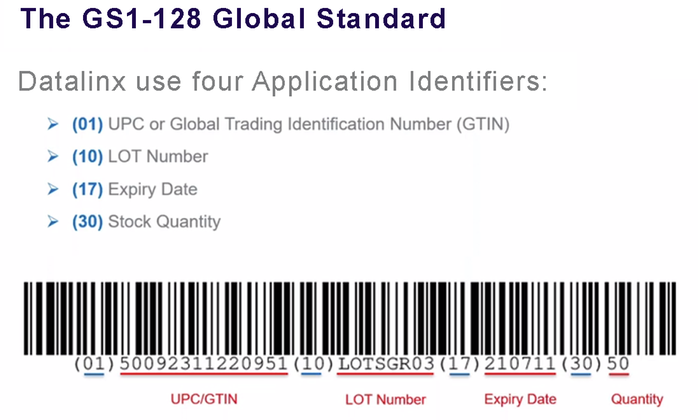